What is Automated Visual Inspection?
Automated Visual Inspection refers to the use of cameras, sensors, and sophisticated software algorithms to automatically inspect manufactured products for defects, inconsistencies, or deviations from specifications. Unlike manual inspection, which relies on human vision and judgment, AVI systems use machine vision technology to capture images of products and analyze them against predefined quality criteria.
These systems serve as the production line’s eyes, detecting deformities, contamination, and other abnormalities that might affect product functionality or appearance. Modern AVI solutions can identify defects that are invisible to the human eye, operating at speeds that far exceed manual inspection capabilities.
Key Benefits of Automated Visual Inspection
Implementing Automated Visual Inspection systems offers numerous advantages over traditional quality control methods. These benefits directly impact both operational efficiency and bottom-line results:
- Enhanced accuracy with detection rates exceeding 99% for many applications
- Consistent inspection criteria without human fatigue or subjectivity
- Increased production throughput with real-time inspection
- Comprehensive data collection for quality trend analysis
- Reduced labor costs and reallocation of human resources to higher-value tasks
- Prevention of costly recalls and brand reputation damage
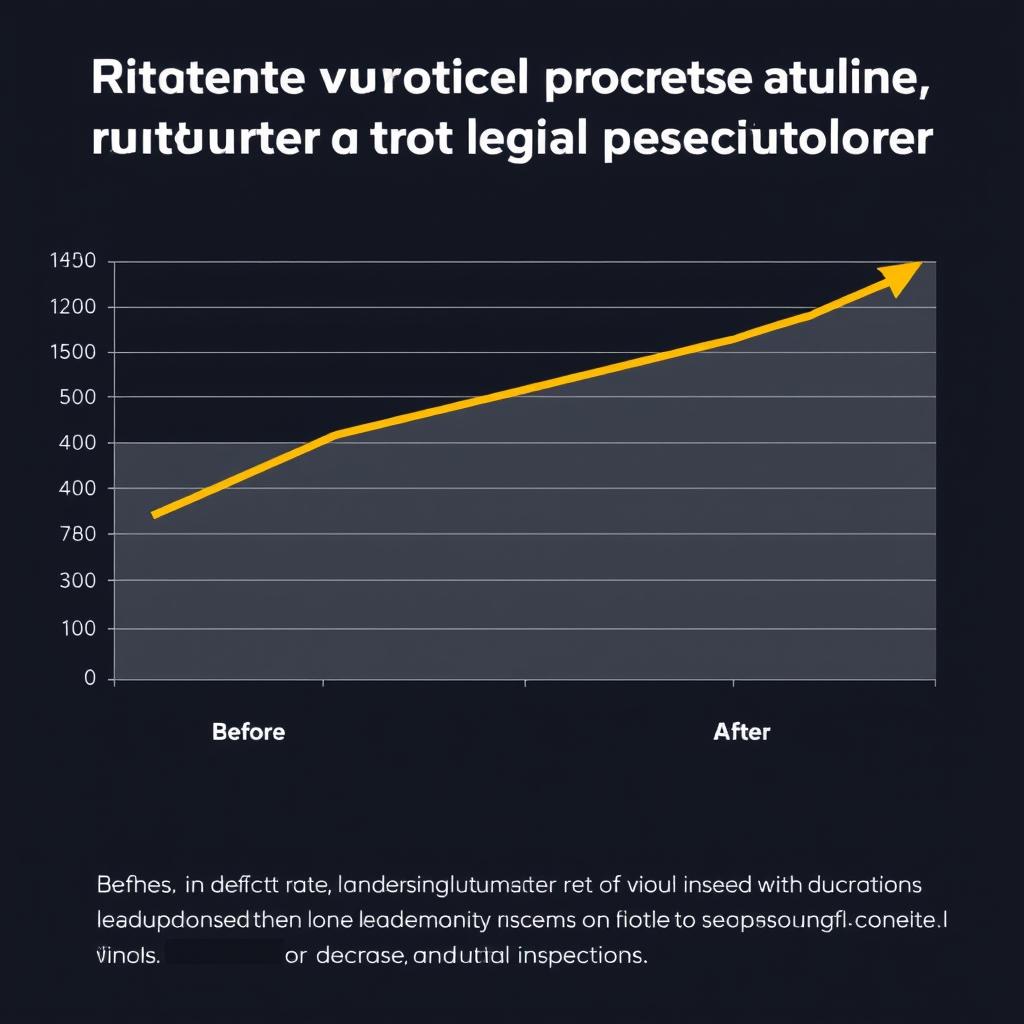
Essential Components of an AVI System
A comprehensive Automated Visual Inspection system consists of several integrated components working together to capture, process, and analyze visual data. Understanding these components is crucial for successful implementation:
Imaging Hardware
High-resolution cameras, specialized lenses, and proper lighting systems form the foundation of any AVI system. The quality of images captured directly impacts detection accuracy.
Processing Units
Industrial-grade computers with sufficient processing power handle the complex algorithms required for real-time image analysis and defect detection.
Software Algorithms
Advanced software using machine learning and computer vision algorithms that can identify patterns, detect anomalies, and make pass/fail decisions based on predefined criteria.
Integration Systems
AVI systems must seamlessly integrate with existing production lines and manufacturing execution systems (MES). This integration allows for real-time quality control decisions, such as rejecting defective products or adjusting production parameters to prevent further defects.
Data Management
Comprehensive data collection and analysis capabilities enable manufacturers to track quality trends over time, identify recurring issues, and implement preventive measures. This data-driven approach transforms quality control from reactive to proactive.
Industry Applications of Automated Visual Inspection
Automated Visual Inspection systems have found applications across numerous industries, each with unique requirements and challenges:
Automotive Manufacturing
In automotive production, AVI systems inspect everything from surface finishes and paint quality to component assembly and weld integrity. These systems can detect microscopic cracks, improper alignments, and other defects that might compromise vehicle safety or appearance.
Electronics Production
For electronic components and PCBs, automated inspection verifies solder joint quality, component placement, and surface defects. The precision required in modern electronics makes automated inspection essential for maintaining quality standards.
Pharmaceutical Packaging
In pharmaceutical manufacturing, AVI ensures correct labeling, package integrity, and product appearance. These systems help maintain compliance with strict regulatory requirements while preventing potentially dangerous packaging errors.
Food and Beverage
AVI systems in food production detect foreign objects, verify packaging integrity, and ensure consistent product appearance. These applications help maintain food safety standards while reducing waste and recalls.
Medical Device Manufacturing
For medical devices, automated inspection verifies critical dimensions, surface quality, and assembly integrity. The high stakes in medical applications make reliable inspection systems essential for patient safety.
Implementation Challenges and Solutions
While the benefits of Automated Visual Inspection are clear, implementation comes with several challenges that manufacturers must address:
Implementation Challenges
- Initial investment costs for hardware and software
- Integration with existing production systems
- Training requirements for operators and maintenance staff
- Developing appropriate inspection criteria and thresholds
- Managing environmental variables like lighting and vibration
Effective Solutions
- Phased implementation to distribute costs and validate ROI
- Working with experienced system integrators
- Comprehensive training programs and documentation
- Iterative development of inspection parameters
- Controlled environment design for consistent results
Key Implementation Steps
- Conduct a thorough assessment of current quality control processes and defect types
- Define clear inspection criteria and acceptable quality levels
- Select appropriate hardware components based on product characteristics
- Develop and train software algorithms using representative product samples
- Integrate the AVI system with production line controls and data systems
- Validate system performance against manual inspection results
- Train operators and maintenance personnel on system operation
- Implement continuous improvement processes for ongoing optimization
Future Trends in Automated Visual Inspection
The field of Automated Visual Inspection continues to evolve rapidly, with several emerging trends poised to further transform quality control in manufacturing:
Advanced AI and Deep Learning
Next-generation AVI systems leverage deep learning neural networks that can identify complex defect patterns without explicit programming. These systems improve over time as they process more images, continuously enhancing detection accuracy.
Edge Computing Integration
Processing visual data at the edge—directly on or near the production line—reduces latency and enables real-time decision making. This approach minimizes bandwidth requirements while improving system responsiveness.
IoT and Connected Systems
Integration with IoT platforms allows AVI systems to communicate with other production equipment, enabling automated adjustments to manufacturing parameters when quality issues are detected.
Predictive Quality Analytics
Advanced analytics applied to inspection data can predict potential quality issues before they occur, allowing for preventive maintenance and process adjustments that maintain consistent product quality.
Augmented Reality Assistance
AR technologies are beginning to complement AVI systems by providing visual guidance to operators when manual intervention is required, highlighting detected defects and suggesting corrective actions.
Calculating ROI for Automated Visual Inspection
Investing in Automated Visual Inspection technology represents a significant capital expenditure that requires proper financial justification. A comprehensive ROI analysis should consider both direct cost savings and indirect benefits:
Direct Cost Factors
- Reduction in quality control labor costs
- Decreased scrap and rework expenses
- Lower warranty claim and return costs
- Reduced risk of costly product recalls
Indirect Value Factors
- Improved brand reputation from consistent quality
- Increased production capacity and throughput
- Enhanced ability to meet regulatory requirements
- Valuable quality data for continuous improvement
Cost/Benefit Category | Typical Range | Calculation Method |
Initial System Investment | $50,000 – $250,000+ | Hardware, software, integration, and training costs |
Labor Savings | 30% – 80% reduction | Current inspection labor cost × reduction percentage |
Defect Reduction | 40% – 90% improvement | Current defect cost × improvement percentage |
Throughput Increase | 15% – 35% improvement | Additional units × profit margin per unit |
Case Study: Successful AVI Implementation
“Implementing an Automated Visual Inspection system reduced our defect rate by 78% while increasing production throughput by 23%. The system paid for itself within 14 months and continues to deliver value through improved quality and reduced labor costs.”
Implementation Overview
A mid-sized automotive parts manufacturer was struggling with inconsistent quality control and high inspection labor costs. Their manual inspection process was unable to keep pace with production demands, resulting in occasional defective products reaching customers.
Challenges
- High variability in manual inspection results
- Increasing labor costs for quality control
- Production bottlenecks at inspection stations
- Customer complaints about inconsistent quality
Solution
- Multi-camera AVI system with specialized lighting
- Custom machine learning algorithms for specific defect types
- Integration with production line control systems
- Comprehensive operator training program
Results
Conclusion: The Future of Quality Control
Automated Visual Inspection represents a significant advancement in manufacturing quality control, offering unprecedented accuracy, consistency, and efficiency. As technologies continue to evolve, AVI systems will become increasingly sophisticated, accessible, and integral to modern manufacturing operations.
For manufacturers looking to remain competitive in today’s quality-conscious market, implementing Automated Visual Inspection is no longer just an option—it’s becoming a necessity. The combination of improved quality, reduced costs, and enhanced production capacity delivers a compelling return on investment that forward-thinking companies cannot afford to ignore.
By carefully assessing your specific requirements, selecting appropriate technologies, and working with experienced implementation partners, you can successfully navigate the transition to automated inspection and realize the substantial benefits these systems offer.
Ready to improve your quality control?
Our experts can help you implement an Automated Visual Inspection system tailored to your manufacturing process.
Not sure which AVI solution fits your industry?
Our industry specialists can assess your specific requirements and recommend the optimal inspection configuration.
Stay ahead with cutting-edge inspection technology
Our team keeps pace with the latest developments in Automated Visual Inspection to deliver state-of-the-art solutions for your manufacturing challenges.
Ready to transform your quality control process?
Contact our team today to discuss how Automated Visual Inspection can benefit your specific manufacturing operation.
Frequently Asked Questions
How does Automated Visual Inspection compare to manual inspection?
Automated Visual Inspection offers several advantages over manual inspection, including consistent application of inspection criteria, higher detection rates for subtle defects, faster processing speeds, and continuous operation without fatigue. While manual inspection may still be necessary for certain complex judgments, AVI systems significantly outperform human inspectors in most routine quality control applications.
What types of defects can Automated Visual Inspection systems detect?
Modern AVI systems can detect a wide range of defects, including dimensional variations, surface flaws (scratches, dents, discoloration), assembly errors, missing components, incorrect labeling, and contamination. The specific detection capabilities depend on the hardware configuration, lighting setup, and software algorithms implemented in the system.
How long does it typically take to implement an AVI system?
Implementation timelines vary based on complexity, but typically range from 3-6 months for a complete deployment. This includes assessment, system design, hardware installation, software configuration, integration with existing systems, testing, and operator training. Phased implementations can allow for earlier benefits while spreading out the investment.