Visual inspection remains a fundamental quality control method across industries
What Is Visual Inspection and Why Is It Critical?
Visual inspection is a non-destructive testing (NDT) method that involves the direct observation of a component to detect surface discontinuities, defects, or deviations from specifications. As the simplest and most fundamental form of quality control, it often serves as a preliminary step before applying more complex testing methods.
The primary objectives of visual inspection in industrial applications include:
- Detecting surface defects such as cracks, corrosion, and porosity
- Verifying dimensional accuracy and alignment
- Evaluating weld quality and integrity
- Identifying assembly errors or missing components
- Supporting other NDT methods by pinpointing areas requiring further examination
Pro Tip: Even with advanced automated inspection systems, trained human inspectors remain invaluable for detecting subtle defects that automated systems might miss. The best quality control programs combine human expertise with technological tools.
Key Visual Inspection Methods
Visual inspection techniques can be categorized based on how inspectors view and interact with the test object. Each method has specific applications, advantages, and limitations that quality managers should understand when developing inspection protocols.
Direct Visual Testing (DVT)
Direct visual testing involves the inspector physically examining the object with the naked eye or simple magnification tools. This method requires direct line-of-sight access to the inspection area and appropriate lighting conditions.
DVT is typically used when the test surface is easily accessible and visible without complex equipment. For example, inspecting welds on a flat surface where the inspector can directly view the area with or without a magnifying glass.
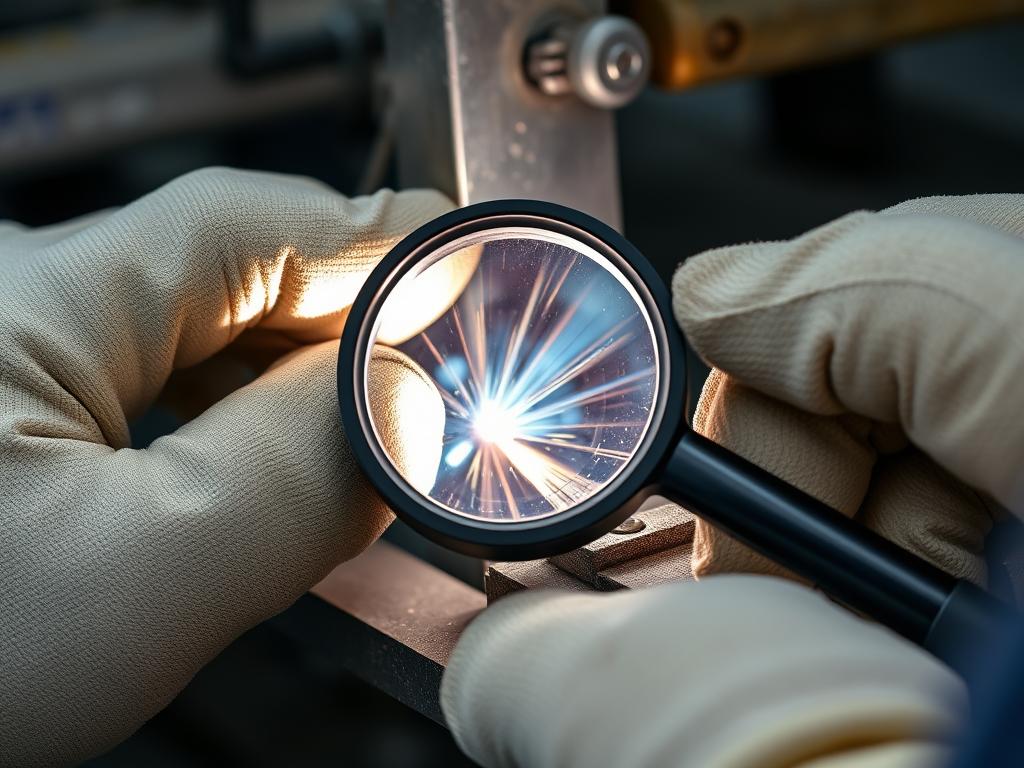
Remote Visual Inspection (RVI)
Remote visual inspection utilizes specialized optical instruments to examine areas that are difficult or dangerous to access directly. This method is essential for confined spaces, hazardous environments, or internal components that cannot be directly observed.
RVI is typically employed when inspecting the internal surfaces of pipes, pressure vessels, turbines, or other confined spaces. For example, using a borescope to inspect the interior of an aircraft engine without disassembly.
Manual vs. Automated Visual Inspection
Beyond the direct/remote distinction, visual inspection can be conducted manually by trained inspectors or through automated systems using advanced imaging technologies:
Inspection Type | Description | Best Applications | Limitations |
Manual Inspection | Performed by trained personnel using visual observation and simple tools | Complex surfaces, subjective quality criteria, low-volume production | Fatigue, inconsistency between inspectors, slower process |
Semi-Automated | Human-operated equipment with digital imaging and analysis support | Medium-volume production, complex but consistent criteria | Initial setup costs, requires skilled operators |
Fully Automated | Computer vision and AI-powered systems that detect defects without human intervention | High-volume production, consistent criteria, repetitive tasks | High implementation cost, limited flexibility for new defect types |
Modern automated visual inspection systems combine multiple cameras, specialized lighting, and AI-powered defect recognition
Essential Visual Inspection Tools & Technologies
The effectiveness of visual inspection depends significantly on the tools and technologies employed. From simple magnifiers to advanced imaging systems, quality professionals have access to a wide range of equipment designed for different inspection scenarios.
Basic Inspection Tools
- Magnifying glasses and loupes
- Inspection mirrors
- Measuring devices (calipers, micrometers)
- Surface comparators
- Specialized lighting (flashlights, UV lights)
Optical Instruments
- Borescopes and fiberscopes
- Video probes and cameras
- Microscopes (digital and optical)
- Endoscopes for confined spaces
- Articulating video probes
Advanced Technologies
- Drone-based inspection systems
- 3D imaging and photogrammetry
- Thermal imaging cameras
- AI-powered defect recognition
- Augmented reality inspection aids
Comparison of Visual Inspection Tools by Application
Tool Category | Cost Range | Accuracy Level | Best For | Limitations |
Basic Hand Tools | $10-$500 | Moderate | Surface defects, general inspection | Dependent on inspector skill, limited magnification |
Borescopes & Video Probes | $500-$15,000 | High | Confined spaces, internal components | Limited maneuverability in complex geometries |
Digital Microscopes | $200-$5,000 | Very High | Micro-defects, precision components | Limited field of view, requires stable platform |
Drone Systems | $2,000-$50,000 | Moderate to High | Large structures, hazardous areas | Weather dependent, requires skilled operator |
AI-Powered Systems | $10,000-$250,000 | Very High | High-volume production, consistent criteria | High implementation cost, requires training data |
Visual Inspection Best Practices
Standardized procedures and optimal environmental conditions are essential for consistent visual inspection results
Environmental Controls
The inspection environment significantly impacts the effectiveness of visual inspection. Proper controls include:
- Lighting: Maintain a minimum of 500 lux for general inspection tasks and 1000+ lux for precision work. Use diffused lighting to minimize glare and shadows.
- Viewing Angle: Position inspectors within 24 inches (600 mm) of the inspection surface with a viewing angle of no less than 30° to optimize visibility.
- Ergonomics: Design inspection stations to minimize fatigue with adjustable seating, proper work height, and tools that reduce physical strain.
- Background: Use contrasting backgrounds to enhance defect visibility—light backgrounds for dark objects and vice versa.
- Cleanliness: Ensure both the inspection area and the items being inspected are clean and free from contaminants that could obscure defects.
Pro Tip: For critical inspections, implement the “four-eyes principle” where two inspectors independently examine the same item to reduce the risk of missed defects.
Inspector Training and Certification
The human element remains crucial in visual inspection, even with advanced technologies. Effective training programs should include:
- Formal Certification: Industry-recognized certifications such as Certified Welding Inspector (CWI) or ASNT Visual Testing Level II provide standardized knowledge.
- Defect Recognition: Training with actual defect samples and reference standards to develop pattern recognition skills.
- Vision Testing: Regular vision acuity and color perception testing to ensure inspectors can effectively detect visual anomalies.
- Continuous Learning: Ongoing training to maintain skills and learn new inspection techniques as technologies evolve.
- Cross-Training: Familiarity with multiple inspection methods to understand how visual inspection complements other NDT techniques.
Effective training with reference standards is essential for developing inspector proficiency
Documentation and Standardization
Consistent documentation ensures repeatability and traceability in the inspection process:
- Written Procedures: Develop detailed inspection procedures that specify acceptance criteria, inspection methods, and required tools.
- Reference Standards: Maintain calibrated reference samples showing acceptable and unacceptable conditions for comparison.
- Digital Documentation: Use digital systems to record inspection results, including photos of defects for future reference and training.
- Traceability: Implement systems to track which items were inspected, by whom, when, and with what results.
- Regular Audits: Conduct periodic reviews of inspection processes to identify improvement opportunities and ensure compliance with standards.
Case Study: AI-Powered Visual Inspection Success
How Company X Reduced Defects by 30% Using AI Visual Inspection
Company X, a mid-sized automotive components manufacturer, was struggling with inconsistent quality in their precision machined parts. Manual visual inspection was time-consuming and subject to inspector fatigue, resulting in customer complaints and costly warranty claims.
The Challenge
- High-volume production (50,000+ parts daily) requiring 100% inspection
- Complex surface finish requirements difficult to standardize
- Inconsistent results between different inspectors and shifts
- Increasing customer quality requirements
The Solution
Company X implemented an AI-powered visual inspection system that combined high-resolution cameras, specialized lighting, and machine learning algorithms trained on thousands of sample images of both acceptable and defective parts.
The AI system was trained to recognize 27 different defect types with 99.7% accuracy
The Results
- 30% reduction in customer-reported defects within 3 months
- 40% increase in inspection throughput
- 22% decrease in quality-related costs
- Redeployment of inspectors to higher-value quality improvement activities
- Comprehensive defect data collection enabling root cause analysis
Common Visual Inspection Challenges & Solutions
Despite its fundamental importance, visual inspection faces several challenges that can impact its effectiveness. Understanding these challenges and implementing appropriate solutions is essential for maintaining inspection quality.
Challenges
- Inspector Fatigue: Prolonged inspection tasks lead to decreased attention and missed defects.
- Subjective Interpretation: Different inspectors may interpret the same visual data differently.
- Complex Geometries: Intricate parts with multiple surfaces are difficult to inspect thoroughly.
- Inaccessible Areas: Internal components or confined spaces may be difficult to view directly.
- Varying Lighting Conditions: Changes in illumination can mask or falsely indicate defects.
- High-Volume Inspection: Large quantities of items require significant time and resources.
Solutions
- Rotation Schedules: Implement regular breaks and task rotation to combat fatigue.
- Standardized Criteria: Develop clear, objective acceptance standards with visual references.
- 3D Imaging: Use photogrammetry and 3D scanning for complex geometries.
- Remote Visual Tools: Deploy borescopes and video probes for inaccessible areas.
- Controlled Lighting: Standardize illumination with consistent, appropriate lighting.
- Automated Systems: Implement AI and computer vision for high-volume inspection.
Future Trends in Visual Inspection
The field of visual inspection continues to evolve rapidly, driven by advances in imaging technology, artificial intelligence, and connectivity. Understanding these emerging trends can help quality professionals prepare for the future of inspection.
Augmented reality is transforming visual inspection by overlaying reference data and guidance directly in the inspector’s field of view
Emerging Technologies
AI/ML Integration
Artificial intelligence and machine learning are revolutionizing visual inspection through:
- Automated defect recognition with increasing accuracy
- Predictive analytics to anticipate quality issues
- Self-learning systems that improve over time
- Natural language processing for automated reporting
Augmented Reality
AR technologies are enhancing human inspector capabilities with:
- Smart glasses displaying inspection checklists
- Real-time overlay of reference standards
- Visual guidance for inspection sequences
- Remote expert assistance for complex issues
Connected Inspection
IoT and cloud technologies are creating integrated inspection ecosystems:
- Real-time data sharing across global operations
- Digital twins for virtual inspection planning
- Blockchain for inspection record verification
- Mobile-first inspection platforms for field use
Industry Adoption Outlook
The implementation of advanced visual inspection technologies varies significantly by industry, with aerospace and automotive leading adoption while other sectors follow at different rates:
Industry | Current Adoption Level | Primary Technologies | Future Outlook |
Aerospace | High | 3D scanning, AI defect detection, AR-assisted inspection | Full integration of AI with human oversight for critical components |
Automotive | High | Automated vision systems, robot-assisted inspection | Fully automated inspection lines with minimal human intervention |
Electronics | Very High | Automated optical inspection (AOI), X-ray systems | Integration of multiple inspection technologies in single systems |
Oil & Gas | Medium | Drone inspection, remote visual tools | Autonomous robots for hazardous area inspection |
Food & Beverage | Medium-Low | High-speed vision systems, hyperspectral imaging | AI-powered contamination detection and sorting |
Pro Tip: When implementing new visual inspection technologies, start with pilot projects in critical areas where the ROI is most evident. Use the data and experience gained to guide broader implementation.
Conclusion: Building an Effective Visual Inspection Program
Visual inspection remains a cornerstone of quality assurance across industries, combining the irreplaceable judgment of trained inspectors with increasingly sophisticated technologies. As we’ve explored throughout this guide, effective visual inspection programs balance traditional methods with emerging technologies to achieve optimal results.
The key elements of a successful visual inspection program include:
- Well-defined inspection criteria and procedures
- Properly trained and certified inspection personnel
- Appropriate tools and technologies for specific inspection needs
- Controlled environmental conditions that optimize visibility
- Comprehensive documentation and traceability systems
- Continuous improvement through data analysis and process refinement
By implementing the methods, tools, and best practices outlined in this guide, quality assurance managers can develop robust visual inspection programs that detect defects early, reduce quality costs, and ultimately deliver superior products to customers.
Continuous improvement through data analysis is essential for evolving visual inspection programs